First I started making the bulkhead templates, I tried to find 1/2
inch plywood, found them to be too costly, so worked with 1/4 inch 3' x
6' sheet. Finished drawing and cutting them up in a few days. I drew the
plots both on the left and right hemispheres. I suggest the plot be done
on a paper, one side as found in the plans, then doubling it on the
plywood with reference to the center vertical line. This will result in
a more symmetrical shape. The completed bulkhead templates are seen in
the background.
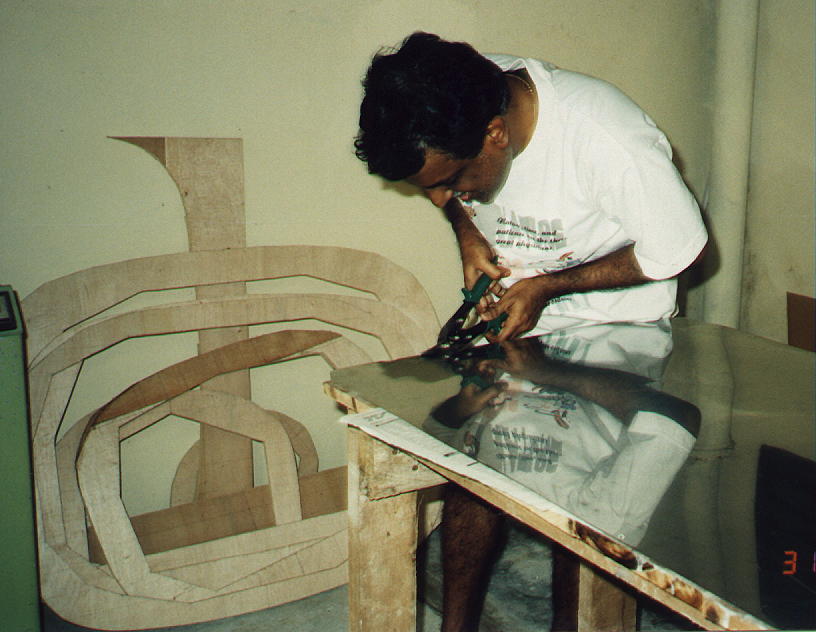
After several months of hunting I got one sheet of
2024-T3 0.040" sheet. I followed the cutting plan provided by the
designer in the plans. I was so scared that I may make a slip while
cutting it, this sheet cost me a bomb. So I requested my Guru named
Muthalib (he had built two RV6 and a KR2 already) to help me initiate
the job. Also witnessing this opening ceremony is Victor Craig (A
Canadian building a Murphy Rebel here at the KITFAM...sorry Craig
reflection of your face on the sheet is not that clear). Just like any
new venture I had to dirty my hands and that was done when I started
cutting metal, now after several months I am beginning to think I am a
expert in it.
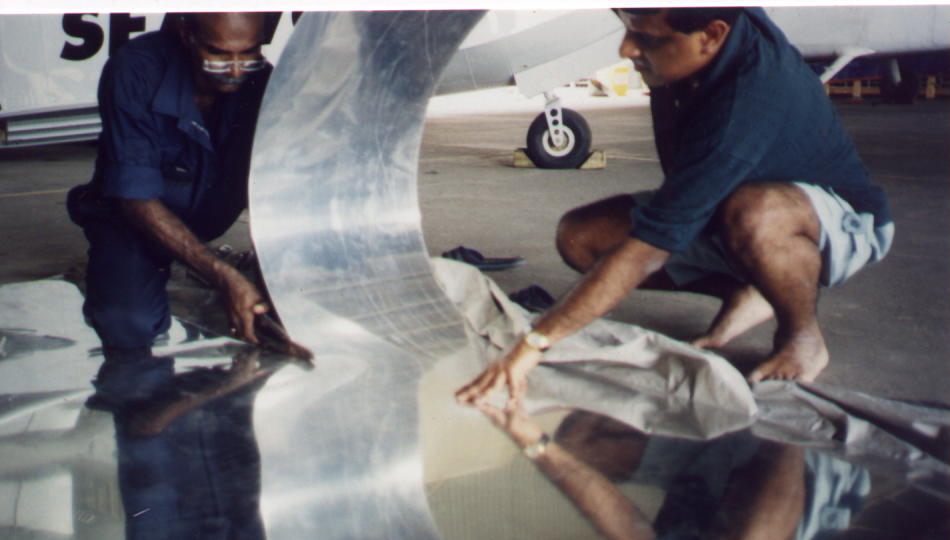
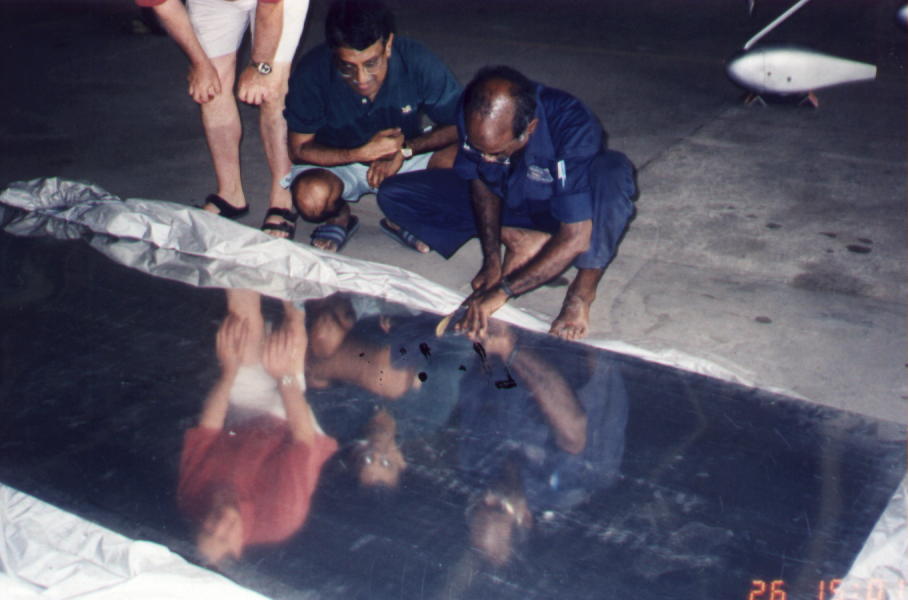
Only four of my bulkheads are made from a single piece
metal, the remaining five are made of two or more pieces. I made full
use of the 0.040" sheet. The cutting plan specifies 1.5 sheet of 4' x
12' 0.040" but I had to use at least two full sheets to make all the
parts that required to be made out of 0.040" thickness metal. Be very
careful while bending the tabs in the Bulkheads. Inspite of checking and
counter-checking several times I bent the tabs in Bulkhead 3 wrongly. I
had to do some recovery processes to save the piece. The plans call for
0.75" flange (outer perimeter) but I was not confident, so I used a 1"
flange, hoping that after drilling the skin attach holes, I can trim
away the excess metal. This is not aiming for zero defect production I
suppose.
Drilling and Deburring the holes and edges is also a new skill I learnt.
My guru Muthalib really grilled me on this, he would call for rework
every time I approach him for a quality check. I left it to my son
Ganesh to deburr the holes for me, as well and minor sanding jobs. The
youngster is not showing much interest in the project. I guess, the
interest will be kindled as soon as the shape of the plane appears in
the workshop, and even more when the engine is installed.